Unlocking the Future of Construction with Non-Destructive Testing (NDT)
- sudarshan bire
- Dec 2, 2024
- 2 min read
In today’s fast-paced construction industry, ensuring structural integrity while maintaining efficiency is paramount. This is where Non-Destructive Testing (NDT) comes into play—a revolutionary approach that has transformed how we assess and maintain structures.
Whether you’re involved in construction, aerospace, oil and gas, or manufacturing, NDT provides invaluable insights into material properties without causing any harm. Let’s dive deeper into what makes NDT the cornerstone of modern engineering.
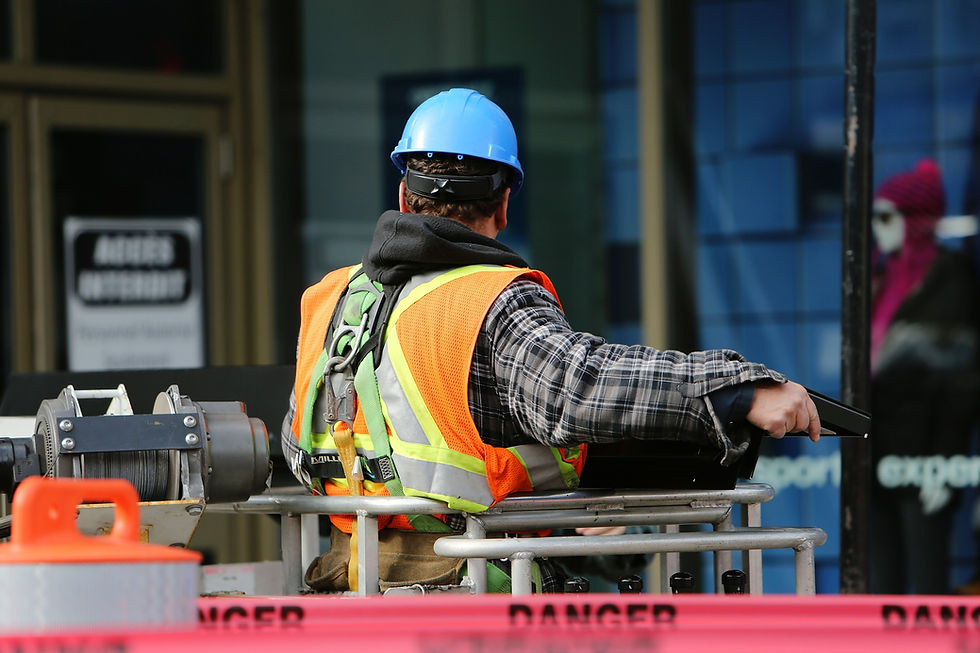
What is Non-Destructive Testing (NDT)?
Non-Destructive Testing refers to a collection of techniques used to evaluate the properties of materials, components, or systems without causing damage. It ensures that structures are safe, reliable, and compliant with industry standards.
Why is NDT Important?
Safety Assurance: Identifies potential flaws before they lead to failures.
Cost-Effectiveness: Minimizes downtime by detecting issues early.
Quality Control: Verifies the integrity of materials and construction processes.
Regulatory Compliance: Meets global standards like ASME, ASTM, and ISO.
Types of Non-Destructive Testing Techniques
1. Ultrasonic Testing (UT):
Uses high-frequency sound waves to detect internal defects.
Commonly used in welding inspections, pipeline evaluations, and composite testing.
2. Radiographic Testing (RT):
Employs X-rays or gamma rays to identify internal flaws.
Ideal for inspecting welded joints and castings.
3. Magnetic Particle Testing (MT):
Detects surface and near-surface discontinuities in ferromagnetic materials.
Often used for bridge inspections and automotive parts testing.
4. Dye Penetrant Testing (PT):
Highlights surface cracks using a liquid dye.
Widely applied in metal fabrication and aviation maintenance.
5. Eddy Current Testing (ECT):
Uses electromagnetic induction to detect surface and sub-surface defects.
Popular in railway inspections and aerospace applications.
6. Visual Testing (VT):
The simplest and most direct form of NDT using tools like borescopes.
Essential for preliminary inspections and routine maintenance.
Applications of NDT in Construction
Structural Health Monitoring: Ensures the stability of bridges, dams, and high-rise buildings.
Pipeline Inspections: Identifies corrosion, cracks, and leaks in pipelines.
Weld Integrity Checks: Verifies the strength and quality of welded joints.
Concrete Assessments: Detects voids, honeycombing, and rebar placement in concrete structures.
Benefits of Using NDT in Construction
Reduced Risk of Failures: Detects flaws before they escalate into catastrophic events.
Eco-Friendly Approach: Prevents waste by minimizing destructive testing methods.
Enhanced Productivity: Keeps projects on schedule by identifying issues swiftly.
NDT Industry Trends in 2024 and Beyond
AI and Machine Learning Integration: Automating flaw detection with higher precision.
Robotics in NDT: Deploying drones and robotic arms for hard-to-reach areas.
3D Imaging and Virtual Reality: Offering more comprehensive visualization of flaws.
Keywords:
Non-Destructive Testing (NDT)
NDT in construction
Structural health monitoring techniques
Ultrasonic testing for pipelines
Radiographic testing in construction
Magnetic particle inspection
Concrete testing methods
Advanced NDT technologies
Cost-effective NDT solutions
Benefits of NDT in engineering
Conclusion
Non-Destructive Testing is no longer just an option—it’s a necessity for industries striving for safety, efficiency, and sustainability. Whether you’re inspecting a skyscraper or a pipeline, NDT ensures every project meets the highest standards of quality and reliability.
Embracing advancements in NDT technologies not only future-proofs your projects but also positions you at the forefront of innovation in a competitive market.
Contact us at SNDT Services Pvt Ltd to explore how our cutting-edge NDT solutions can elevate your next project!

Comments